Description
ABB 500MBA02 1MRB150003R0003 1MRB200053/M
ABB 500MBA02 1MRB150003R0003 is an industrial-grade control module primarily used in distributed control systems (DCS), programmable logic controllers (PLCs), and other industrial automation control applications. Below are its main functions and features:
- Equipped with strong computing capabilities to execute complex logic operations and process control tasks. It may also support real-time data processing to ensure high-precision and low-latency control systems.
- Likely supports industrial bus protocols such as Modbus, Profibus, Ethernet/IP, CANopen, and RS485, enabling efficient communication with other devices. This makes it suitable for data acquisition, remote monitoring, and distributed control in industrial fields.
- Compatible with other I/O modules, facilitating system function expansion. Some modules may support hot-swapping, allowing module replacement without interrupting system operation, thereby improving system availability.
- Features anti-electromagnetic interference (EMI) design, suitable for high-interference environments. It may support a wide temperature range, such as -40°C to 70°C, making it suitable for long-term industrial applications.
- May include fault self-diagnosis and redundancy control functions to ensure stable system operation. It also supports multi-level permission management to prevent unauthorized modifications.
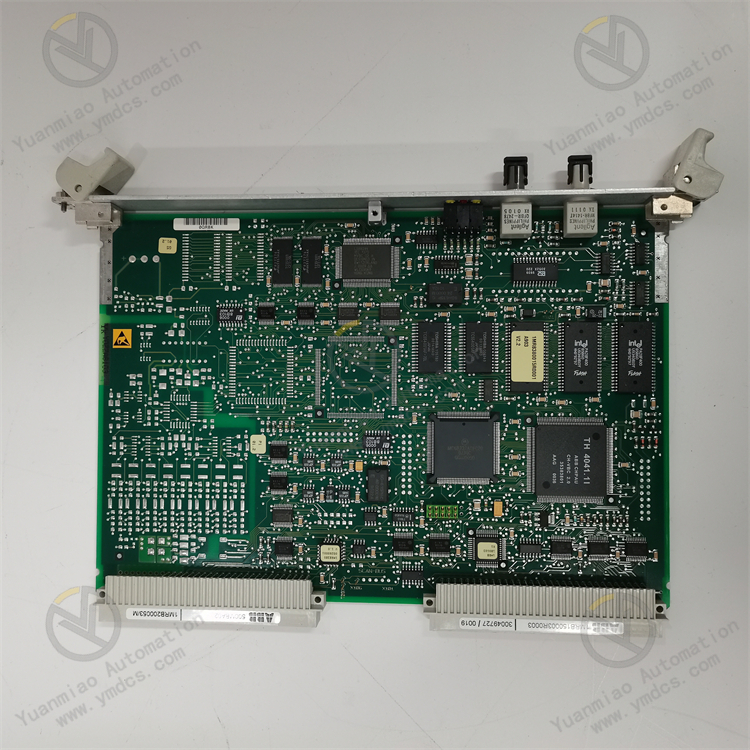
- Processing Capability: Strong computing power to execute complex logic operations and process control tasks, with support for real-time data processing to ensure high-precision and low-latency control systems.
- Protocol Support: Likely supports industrial bus protocols such as Modbus, Profibus, Ethernet/IP, CANopen, and RS485 for efficient communication with other devices, suitable for data acquisition, remote monitoring, and distributed control in industrial fields.
- Modular Design: Compatible with other I/O modules for easy system function expansion. Some modules may support hot-swapping to replace modules without system downtime, enhancing availability.
- Anti-Interference: Anti-electromagnetic interference (EMI) design for high-interference environments.
- Operating Temperature: Wide temperature range support, such as -40°C to 70°C, for long-term industrial applications.
- Fault Diagnosis: May include fault self-diagnosis and redundancy control to ensure stable system operation.
- Permission Management: Supports multi-level permission management to prevent unauthorized modifications.
- The external 380V AC voltage is converted to DC via a rectification circuit, typically composed of components like diodes or thyristors. This process utilizes the unidirectional conductivity of diodes to allow AC current to flow in one direction, forming a pulsating DC voltage. The pulsating DC voltage is then smoothed into a relatively stable 510V DC voltage through a filter circuit (usually using components like capacitors or inductors), providing a stable DC power supply for the subsequent inversion stage.
- The smooth DC voltage is converted into an adjustable AC voltage (in both frequency and voltage) via inverter devices such as insulated gate bipolar transistors (IGBTs). IGBTs work by controlling their gate signals to turn on and off according to a specific pattern, thereby "cutting" the DC voltage into pulse sequences of different widths. After appropriate filtering and processing, these pulse sequences yield AC voltages with variable frequencies and voltages. The voltage adjustment range is typically 0V–380V, and the frequency adjustment range is 0Hz–600Hz. By changing the frequency and amplitude of the output AC voltage, stepless speed regulation control of motors is achieved to meet diverse industrial application requirements.
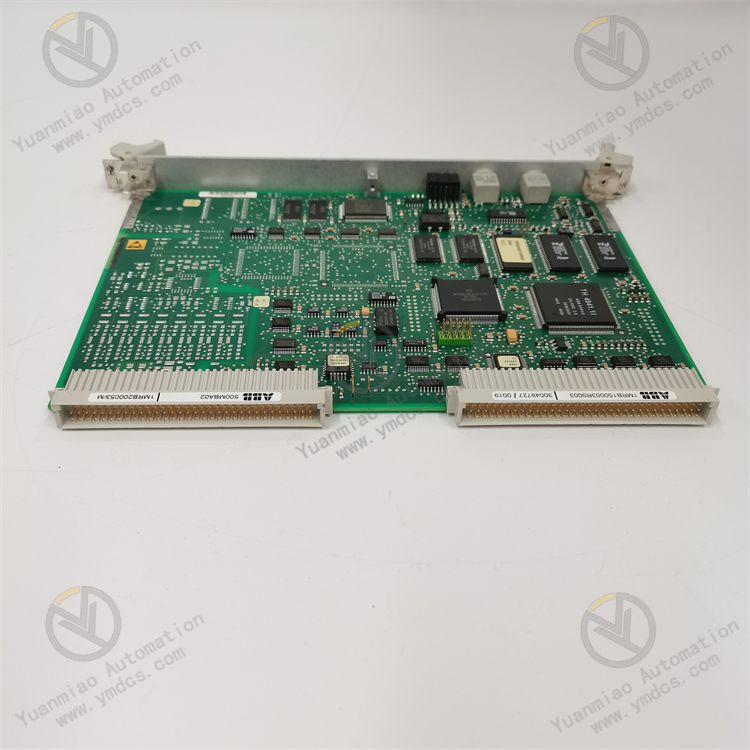
- Ensure the device is correctly installed in the corresponding system, with secure and compliant connections for pipes, cables, etc. Check that the power supply is stable and the voltage matches the device's rated voltage. Ensure operators are familiar with relevant safety regulations and have the necessary qualifications.
- Access parameter settings via the device's operation interface or host computer software based on actual application needs. Parameters may include measurement range, flow unit, time interval, alarm threshold, etc. Read the device manual carefully and set parameters correctly to ensure accurate operation.
- Press the device's power button or issue corresponding control commands to start the device after confirming preparation and parameter settings are complete. The device will typically perform a self-check to verify the integrity of its hardware and software. Observe the display screen or status indicators for error messages.
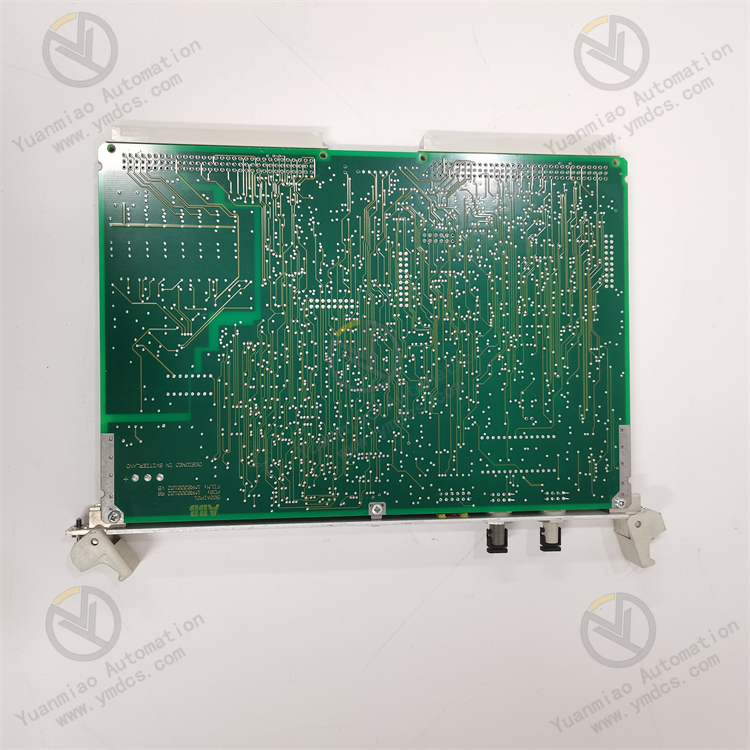
- During operation, closely monitor real-time data on the display (e.g., flow rate, temperature, pressure, if applicable) to ensure measurements are stable and consistent with actual working conditions. Also, pay attention to any abnormal sounds, vibrations, or odors, and shut down the device immediately for inspection if issues are detected.
- Regularly calibrate the device using standard flow meters or other known reference devices to ensure measurement accuracy. Clean the device's sensors and housing regularly to prevent dust and dirt from affecting measurement precision or causing failures. Follow the maintenance manual to periodically inspect performance indicators and replace worn or aged components promptly.
- Record measurement data in relevant tables or systems in a timely manner. Analyzing the recorded data helps track flow trends, evaluate system performance, and identify potential issues or anomalies.
- Follow the device's operation manual for proper shutdown procedures. Generally, stop related processes first, then turn off the device's power. In emergencies, use the emergency stop button, but conduct a comprehensive device inspection afterward to ensure no damage from the abrupt shutdown.
![]()
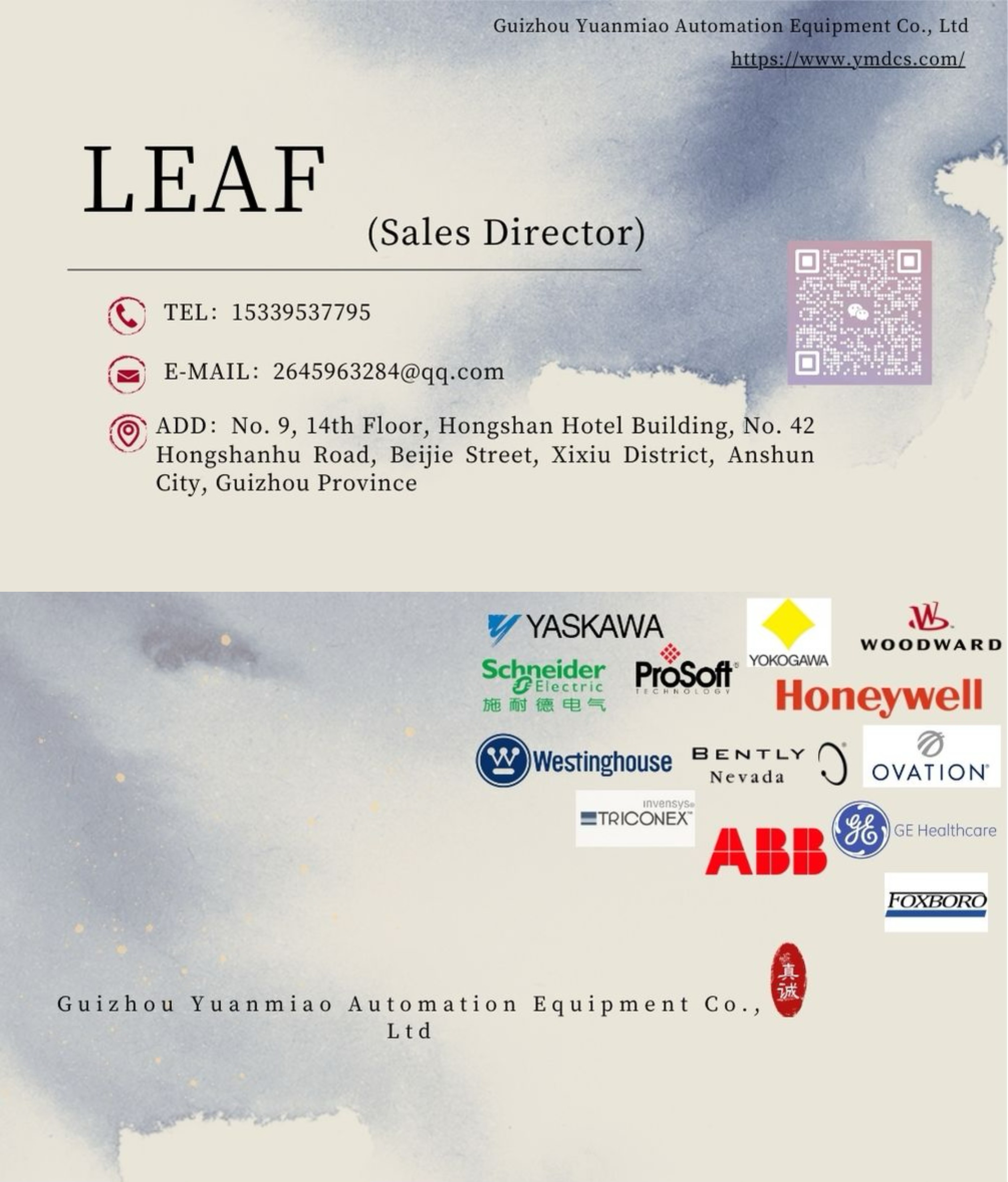