Description
ABB CI840A 3BSE041882R1
The ABB CI840A 3BSE041882R1 is a communication interface module for the ABB AC 800M controller, specifically designed for industrial automation systems to enable high-speed data interaction between the controller and field devices. Its core function is to support the PROFINET communication protocol, acting as a Master or Slave to connect various intelligent devices (such as distributed I/O, variable frequency drives, sensors, etc.), making it suitable for real-time communication and collaborative control in distributed control systems (DCS) and smart manufacturing scenarios.
- Operation Modes:
- Master Mode: Connects to distributed I/O devices (e.g., ABB PM500/PM800 series) and third-party PROFINET slaves (e.g., Siemens ET200SP, Phoenix Contact I/O, etc.).
- Slave Mode: Integrates with higher-level control systems (e.g., PLCs, DCS) to transmit data as a sub-device.
- Protocol Features: Supports PROFINET IO V1, compatible with standard messages, real-time (RT) communication, and isochronous real-time (IRT) functions (hardware-dependent), meeting high-precision synchronization requirements (e.g., motion control, robot collaboration).
- Transmission Rate: Fixed at 100 Mbps (full-duplex), supporting high-speed transmission of large data volumes (e.g., video streams, complex motion commands).
- Data Capacity: Supports a maximum of 1440 bytes input/1440 bytes output, suitable for high-density I/O or extremely real-time scenarios (e.g., automotive production lines, high-speed packaging machinery).
- Redundancy Mechanisms:
- Supports PROFINET Media Redundancy (MRP) and Device Redundancy (PRP), enabling the construction of highly reliable systems with redundant power supplies and controllers.
- Dual-port Ethernet interfaces (RJ45) support ring network topologies, with fault switching time < 200 ms.
- Plug-and-Play: Directly inserts into the AC 800M controller's backplane bus, auto-recognized by ABB Control Builder M software without additional drivers.
- Cross-Vendor Compatibility: Supports importing GSDML files of third-party devices, enabling seamless integration of PROFINET devices from brands like Siemens and Rockwell.
- Distributed Expansion: As a master station, a single module can connect up to 128 PROFINET slaves, supporting hierarchical network architectures (e.g., factory layer - workshop layer - device layer).
- Environmental Adaptability:
- Operating temperature: -20°C ~ +60°C, storage temperature: -40°C ~ +85°C.
- Vibration-resistant (compliant with IEC 60068-2-6) and electromagnetic interference-resistant (compliant with EN 61000 standards), suitable for harsh environments in metallurgy, chemicals, etc.
- Protection Level: IP20 (suitable for installation in control cabinets), supporting rail or backplane mounting.
- LED Status Indicators:
- PWR (Green): Steady on indicates normal power supply; off indicates a power failure.
- RUN (Green): Flashing indicates normal module operation; steady on or off indicates an abnormality (requires checking firmware or configuration).
- LINK/ACT (Yellow): Two lights indicate network connection status (steady on) and data transmission activity (flashing), respectively.
- ERROR (Red): Steady on indicates module faults, slave communication interruptions, or parameter errors.
- Online Hot-Swap: Supports live module replacement (requires a redundant system configuration or ensuring non-operation status).
Parameter | Details |
---|
Communication Protocol | PROFINET IO (Master/Slave mode), compliant with IEC 61158-5-10 standards |
Interface Type | 2 × RJ45 interfaces (10/100 Mbps auto-adaptive, supports Auto-MDI/MDIX) |
Maximum Number of Slaves | Supports 128 PROFINET devices in Master mode |
Data Transmission Mode | Ethernet-based TCP/IP, UDP protocols, supporting real-time data (RT) and isochronous real-time data (IRT) |
Power Requirement | Powered by AC 800M backplane (24V DC, power consumption approx. 300 mA) |
Configuration Software | ABB Control Builder M, Engineering Toolbox (ET) |
Mechanical Dimensions | Conforms to AC 800M module standard dimensions (approx. 100 mm × 160 mm × 40 mm, subject to manual) |
- Automotive Manufacturing: Connects robot controllers (e.g., KUKA, ABB), vision inspection systems, and servo motors to achieve high-precision assembly and motion synchronization.
- Electronics & Semiconductors: Integrates high-speed distributed I/O and vacuum adsorption equipment to meet ultra-clean environment control requirements in cleanrooms.
- Chemical/Oil & Gas: Connects intelligent transmitters, control valves, and safety instrument systems (SIS) via PROFINET, supporting large-scale data acquisition and advanced control algorithms.
- Pharmaceuticals/Food & Beverage: Meets FDA/GMP compliance requirements, enabling real-time monitoring and batch traceability of filling machines and sterilization equipment.
- Smart Grid: Connects relay protection devices and distributed energy sources (e.g., photovoltaic inverters), supporting protocol conversion between IEC 61850 and PROFINET.
- Rail Transit: Connects traction converters and on-board control systems to achieve highly reliable train network communication (e.g., TCN and PROFINET integration).
- Intelligent Buildings: Integrates HVAC systems, elevators, and security equipment to achieve cross-vendor device centralized management and energy optimization via PROFINET.
- Hardware Installation:
- Vertically insert the module into the AC 800M backplane slot, ensuring the latch is locked.
- Use CAT5e/CAT6 shielded twisted-pair cables to connect slave devices; dual ports support star or ring network topologies.
- Software Configuration:
- Add the CI840A module in Control Builder M and configure PROFINET network parameters (e.g., IP address, device name).
- Import GSDML files of third-party slaves, map I/O data to controller variables, and enable real-time communication cycles (e.g., 1 ms synchronization cycles).
Fault Phenomenon | Possible Causes | Solutions |
---|
LINK indicator off | Disconnected network cable or poor contact | Check cable connections and replace network cables or interface modules |
ERROR indicator constant on | Slave offline or configuration errors | Restart slave devices, re-import GSDML files, or check for IP conflicts |
Excessive data delay | High network load or incorrect real-time configuration | Optimize network topology, reduce communication cycles, or enable IRT mode |
Module not recognized | Backplane power failure or outdated firmware | Check backplane voltage and upgrade controller firmware to the latest version |
Dimension | CI840A (PROFINET) | CI810A (PROFIBUS DP) |
---|
Communication Protocol | Industrial Ethernet (PROFINET) | Fieldbus (PROFIBUS DP) |
Transmission Medium | Twisted pair (CAT5e/CAT6) | Shielded twisted pair (PROFIBUS cable) |
Typical Rate | 100 Mbps (high speed) | 9.6 kbps ~ 12 Mbps (medium-low speed) |
Application Scenarios | Large data volume, high-speed synchronization (e.g., robotics) | Traditional automation, long-distance communication (e.g., oil platforms) |
Network Topology | Star, ring (supports MRP redundancy) | Bus, tree |
Maximum Data Capacity | 1440 bytes I/O | 244 bytes I/O |
![]()
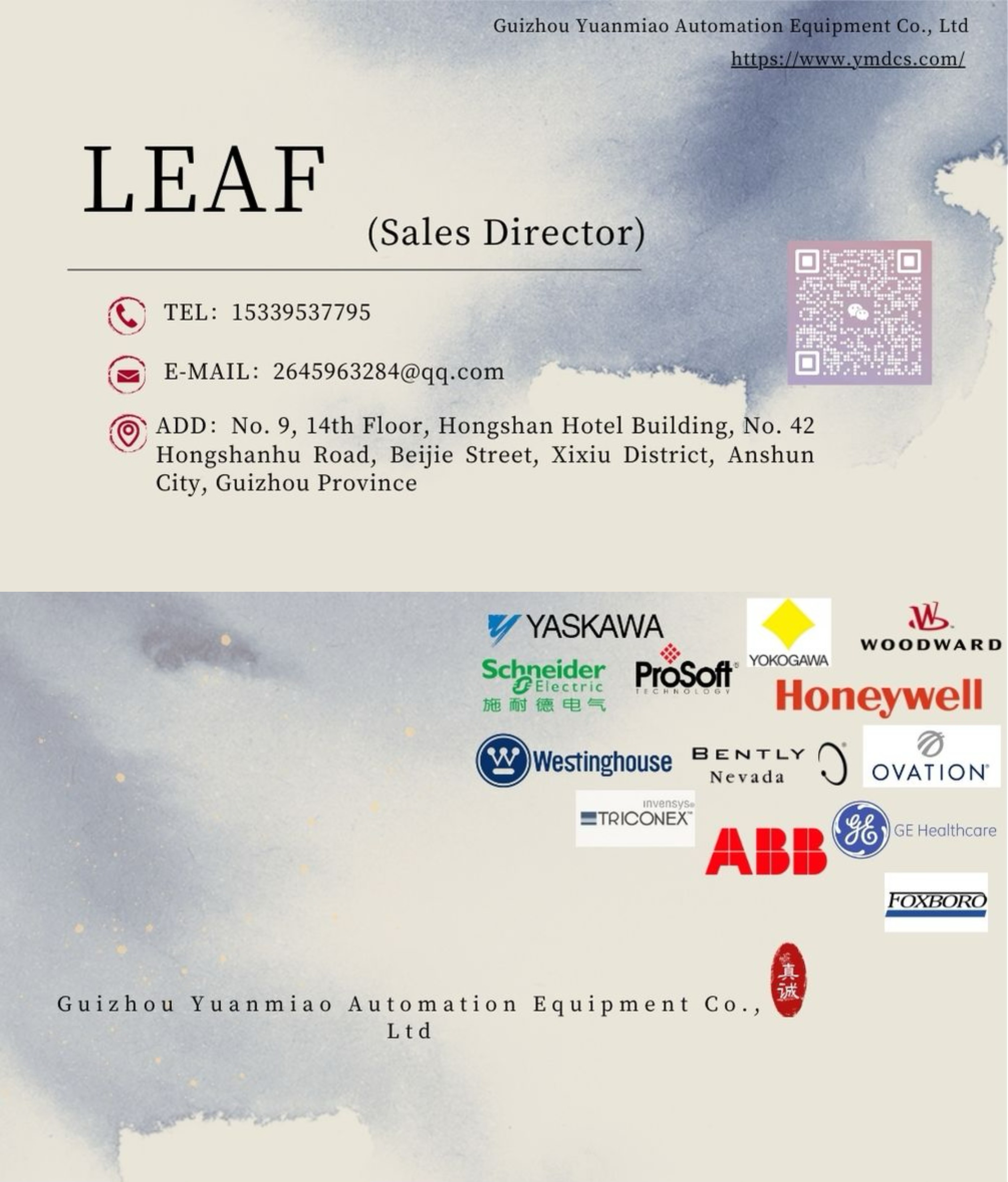